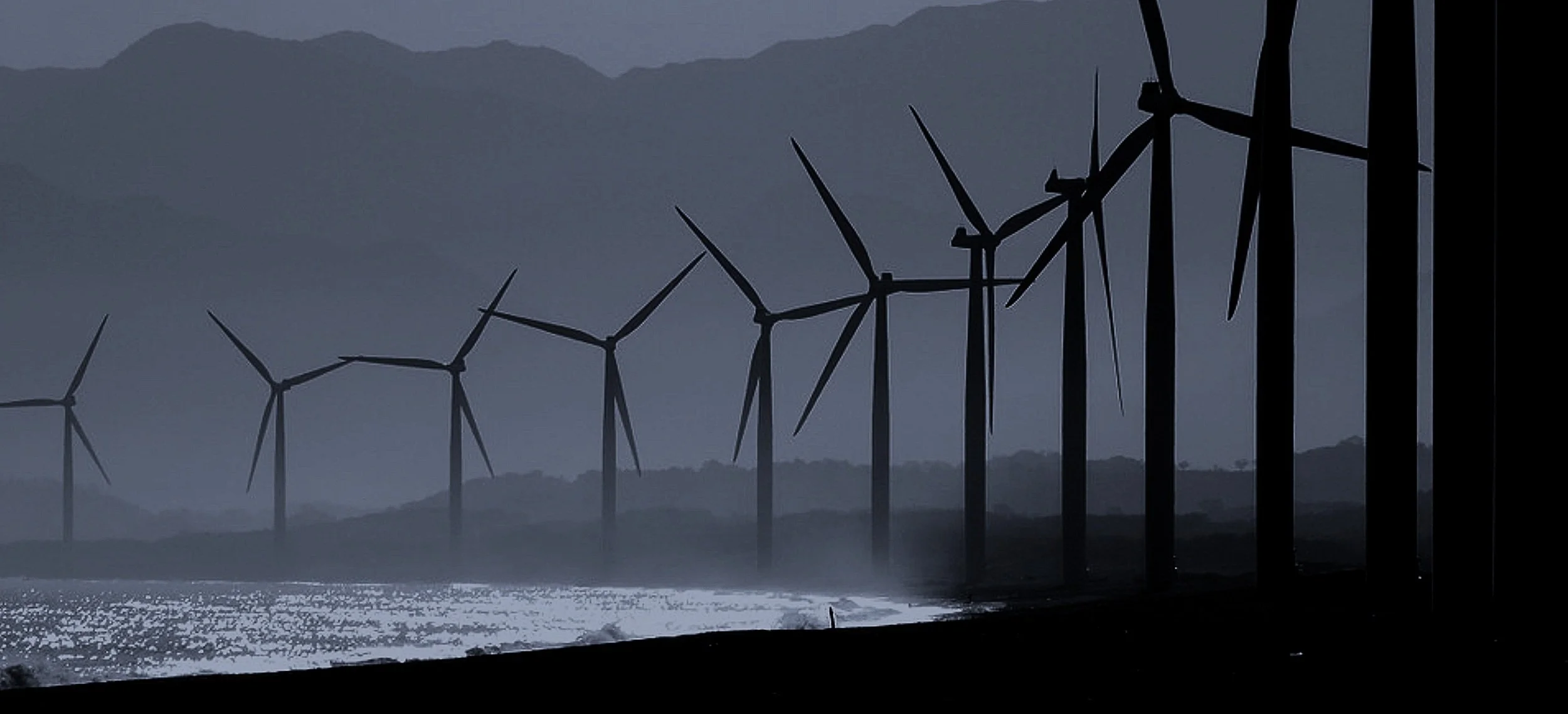
Main Findings
I am a gospel singer. I have a strong voice. When 5 minutes remained for each roundtable, I shouted out and asked all to focus on formulating the main findings from their discussions.
Each table had a QR code and scanning this one took you to the page where the main findings should be shared.
It's perfect lazy reading—valuable sharing from people from 27 countries who gathered in Madrid. You can also understand that quite a few very knowledgeable people are at this event.
The next Owners Roundtable will be held on 12-13 Nov also in Madrid - read more at this link.
Enjoy/Mårten at O2O WIND
The main findings from Madrid can be found as a PDF at this link or below.
Main Findings - Session 1
S1 - Self-performing turbines
Sharing # 1
Not many people are self-performing, only larger operators (MCR, blades, maintenance - still mostly OEM, fear of taking on this and justifying the cost)
Access issues between all OEM for better data visibility (supply chain, BOM, spare parts, failure rates, parameters, set points, compliance, design changes, retrofits)
Call for deviation detection standards for operations: request for detailed changes in software, parameters, performance limits.
Sharing # 2
Challenges and reasons for having self performance turbines:
Supply chain issues
What to take into account/arrange for doing this:
By doing failure mode analysis you can calculate how many spares you want to buy or ask for the failure rate at the supplying party itself.
Check options at different parties than OEM, often OEM provides expensive parts.
Vibration analysis is useful and necessary.
Sourcing together with other parties to have more renegotiation parties, mainly when you are a smaller party
Make sure you have all drawings, technical details, etc.
Make sure you have supply chain agreements.
First 2 years 'knowledge exchange' with site manager, bop manager, taking into account DNP.
For smaller companies, going fully for self-performing can be harder or more expensive; in between steps, we will be going for ISP'er or taking contract excl main components.
Other idea: seperate preventive contract, corrective contract, blade contract.
However, with the above, new forms of managing new challenges come up (like which HSSE procedures to follow)
Consider that with self-performing turbines, you need to pay per software update. Make sure you keep track of software updates.
Sharing # 3
Very informative session, to be able to go for self performance the company will have to develop the necessary skill sets, get the tools needed and develop a supply chain for the spare parts. There is no single solution, it seems, and one needs to keep developing internal systems one by one.
Sharing # 4
Self-performing is a good strategy, but it is not required from Day 1. It is better to make it progressively, beginning with scheduled maintenance, then corrective, and finally MCR. For better operating couple parameters need to be study before such as spare parts management, SCADA system etc
Sharing # 5
It exists evolutive service contracts to go step by step on self performing.
Self-performing is mainly hard on 2 points: RCA and Spare part availability
Sharing # 6
The decision to step into self-performance is complex and depends on many factors. It also depends on the specific situation of the organization.
Sharing # 7
All struggle to get access to all the ingredients needed for self-performance. Documents and experienced personnel are hard to get, and the OEMs know/exploit that. Owners need to get together to create a counterweight to this imbalance.
Sharing # 8
The decision to go into an in-house operational model requires several aspects to be considered beforehand, like supply and chain strategy, access to the control system to manage the data of the assets, documentation and talent management, OEM relation management, etc. If you manage these aspects, it will be an advantage from a financial perspective as well to go into the in-house model.
Sharing # 9
Move to Self-performing in old wtgs as the failure rate is known, and there is a high risk for new wtgs.
The hybrid model works better (don’t cut 100% OEMs)
Oil, grease, particles and cms before moving from FSA to Self-performing
In self-performing mode, You are the decision maker.
Sharing # 10
To start SP, it’s important to have a good knowledge of conditions and, if possible, the failure modes on different components, particularly at the MC level, which will allow us to calculate the failure rate.
We have a good agreement with OEM on SCADA and engineering support.
Get or develop good documentation to do maintenance.
Sharing # 11
It exists evolutive service contract to go step by step on self-performing.
S1 - Market-Driven Operations
Sharing # 1
Price fluctuations have a negative effect on operations.
Budgeting the annual production with price fluctuations is very difficult, so historical data is key.
OEM contracts should be aligned with variable prices.
Owners need to have better control over their data.
Hybrid plants have unique challenges with grid code compliance, so grid study and grid code modelling are key.
Sharing # 2
It is difficult to handle O&M resources and planning under highly fluctuating energy price circumstances.
Perhaps a comprehensive system would include not only Scada data but also CMMS, energy prices, forecasts, etc. is needed.
Sharing # 3
Management of negative hours: possibility to automatize the stops through a merit-order algorithm and the hypervision tool.
Need to be careful about failures following a stop: better not to stop exactly at the tipping point but to include some margin to take into account this risk.
The ancillary services market might be an opportunity for additional revenue generation
Sharing # 4
Revenue-based availability instead of time or energy-based availability
A relationship with the OEM is mandatory in this context, where prices fluctuate. Deemed energy to be borne by OEM
Historical data is the best option so far for budget production
In-house Scada solution to better control
Sharing # 5
Service agreement cannot be priced as EUR/MWh and Energy availability in the future when prices becomes low or even negative. Need to connect towards market prices, question is how?
Overdimensione solar vs wind in hybrid projects. Overdimension solar vs grid capacity.
Master controller for hybrid parks is challenging. Several operators are developing their own master controller since "off the shelf" is not dynamic enough and you want to have a standardised controller.
When you choose which WTG to curtail you can also take the loads into account in case you have some WTG's with higher loads than others.
Create a KPI three so you can see what KPI's are actually influencing the higher level KPI.
Give local techs bonus on a regular basis based on site performance.
Some Chinese OEM's seems to have better performance then western suppliers.
Sharing # 6
Main issue discussed was how to react to negative prices. Active curtailment was discussed, and a key topic was how to perform the curtailment. The different owners have different approaches, which range from using the BRP access to process the instructions directly (in-house).
Main questions that remain are i) how to determine a threshold which makes it profitable to perform the curtailment, ii) whether the active curtailment may have technical implications in the turbines (e.g. some cases have been observed in which after doing curtailment, the turbines suffer some stops, which offset (or even exceed) the gain achieved with the curtailment.
Another topic discussed was the possibility to perform ancillary services, in order to compensate for negative prices, especially during summer months.
Sharing # 7
Not all MWh are created equal - owners need to have an appreciation of the value of the energy being produced at that moment in time.
Trying to schedule O&M works to suit pricing fluctuations requires a crystal ball, and the best approach is to try to secure some flexibility in the O&M contract, potentially incentivising the contractor.
The complexity of hybridised plants is vast, and the industry does not have a supplier of hybrid control systems. BESS can certainly support the situation from a grid compliance perspective, but it adds complexity.
Sharing # 8
Collaboration with BRP can be a solution in a low electricity price market such as Finland or Sweden.
Our company is making new attempts to automate the starting and stopping of wind turbines. This requires extensive preparation, such as databases and algorithms, but it can save huge costs if it works.
Sharing # 9
Price fluctuations is a challenge, especially for hybrid plants and control.
Grid compliance is now considering plant behaviours in a steady condition, which should be upgraded.
Contracts with OEMs should take into account price.
Incentivizing people on-site and in local communities is key to success.
How is BESS entering the game?
Chinese turbines are changing the market and decisions.
Sharing # 10
Prices are changing quickly. All the megawatts do not have the same value.
Master controller is a must in hybrid power plants.
Hybrid power plant should be handled as a one system in grid code compliance tests. All the subsystems should not be tested separately. That idea to be selled to TSOs.
Production budgets need to be updated according to market driven operations.
Sharing # 11
It seems that all parties around the table, from different countries face negative prices.
The approach is different depending on whether or not the company is a BRP.
It seems most stops for negative prices are still manually executed.
It is possible to automate it , but this work is still to do.
S1 - End of Warranty
Sharing # 1
End of warranty difficult with OEM. OEMs have tactics to deal with claims, e.g. wear and tear.
Scope of inspection: various depending on length of warranty term and whether full scope contract is following inspection.
Standards: IEC61400-28 will be issued at the end of 2024. The standard includes a checklist in the appendices.
It is difficult to predict the failure rate accurately when prioritising inspection of specific components. Therefore, the cost of replacement drives owners' priorities.
BSH requires 25% of offshore turbines to be inspected per annum. This can be used as part of an EOW campaign.
Geographical variations between OEM approach to end of warranty and statutory requirements vary from country to country.
Various successes of claims between owners. Use serial defect claims as a negotiating tool, as they are hard to prove. Legal teams can be involved in writing contractual letters, and if there is no positive response from OEM, then a monetary claim can be made for remediation by the owner.
Technical documents are challenging to get if not negotiated in the turbine supply agreement. Even if documentation is in the contract, the OEM will resist this to owners during this time. Detailed documentation is needed for gearbox internal inspections, for example.
Sharing # 2
Before the warranty expires, the inspection methods are CMS treed, visual, borescope, and blade by rope and drone.
Earlier inspection timing by ourselves is important.
Sharing # 3
Two standards relative to lifetime extension include a checklist in the appendix:
o IEC 61400-28
o DNV-ST-0262
Sharing # 4
It is very valuable to share experiences with colleagues.
The information I found most valuable is problems related to the Nordex platform (related to blades).
Related to the problems of my own experience, we shared ideas.
Sharing # 5
Supplier tips:
o Top Seven: https://www.topseven.com/beruehrungslose-blitschutzmessung/
Sharing # 6
Contractual rights to claim for a defect that you know eventually will become a serial defect but that has not reached the threshold limit within the EOW date
Sharing # 7
Some operators struggle to define the inspection regime (DNV & IEC checklists are available), have EoW negotiations, and assess failure rates for self-operating.
They all have difficulty dealing with the Danish OEMs regarding serial defect discussions.
S1 - Leading Edge Erosion
Sharing # 1
Application of LEP should be carried out within the climatic conditions as per the material data sheet
Selection of the most appropriate LEP should be site-specific so as to get the most out of the product
The existing types of LEP are as follows: Liquid coatings, Shells, 3-M tapes
Methods of applications include Robotic solutions (companies - Aerones, Blade Robots, Sparrow), Basket repairs and Rope Access
The commencement of repairs generally starts at category three erosion
LEP products are governed by DNV standards 0171 for Design and 0573 (failure Modes)
Sharing # 2
In my opinion, ELLE shells are still the best option. However, they are challenging to install after construction in less controlled conditions.
Sharing # 3
Site suitability: Owners are lacking in assessment to ensure that the blade supplied by the OEMs suits the site. It is a critical input since OEMs always blame weather conditions (e.g. it rains a lot on that site) for causing unexpected wear and tear (exclusion in O&M contract). Erosion should be part of the site assessment. There are also ways to characterize the site with rain gauges and disdrometers
LEP selection: Shells are the best-performing products on the market. Also, the most expensive ones. This solution might be an overshoot for some sites. LEP should be selected in function of site exposure. Tapes are good solutions but some versions did not perform very well. Issues with tapes when it degrades: hard to remove, creating noise. Coatings: wide panel of solutions. Application is critical, if defects are introduced, coating will not last.
Impact of peformance: Why repairing? 1) Impact on performance of the blade? 2) Impact on performance? 3) Visual impact (community);Owners are trying to identify impact on AEP using operational data. Uncertainty is high. Always depends on blade condition. Trials with LiDAR. Open access model from DTU (SALT)
Durability and Repairs: Best time to repair is when Category 3 damage is reached. When laminate layers are damaged, repair time and cost increase. LEE is usually combined with other types of repairs on the blades. Weather conditions are important to get good quality repairs. Robotics repairs are currently screened by some owners.
Erosion safe mode: Curtailing the turbine to save on AEP degradation or number of repair campaings. Good idea but no one has tested it.
Sharing # 4
Consider rainfall assessment (including droplet size) to be built into turbine supply specification
Tool for energy assessments for LE damage SALT open-source application
Consider strategic RPM reduction to reduce LE damage
Sharing # 5
OEMs are going to a place where they exlcude each time more a more about blade leading edge repair
Erosion shields are good for blade erosion; the key component is a good installation
Erosion could get the water in, and lighting could be an issue. High erosion causes lot of noise
AEP gain from a good reparation leading edge is quite difficult. Uncertainty in the calculation is too high to determine the gain %
Leading-edge repair robots need to be tested to see if they are cost-effective
Sharing # 6
Useful insights around corrective and preventive solutions such as tape-based leading edge protection and coating options.
Experiences shared around polyurethane coatings and 3M tapes as examples.
Services from bladena and aerones also came into the conversation.
Overlapping matters in regards to LPS and de-icing add-ons to be considered when thinking of retrofitting the blades.
Sharing # 7
Leading edge erosion is a larger issue than I thought before the meeting.
I learned that it is very important to do Something at an early stage if starting erosion is seen. And I also learned that inspection is necessary.
There are many types of repair methods, but it is more important to start early than the selection of type.
I also learned that some blades can have very low protection for erosion.
Be also aware when signing a contract if erosion is excluded.
Sharing # 8
LM blades manufactured in China can have deep erosion even after 2 years
feedback about LE-rigid Shield protection
AEP erosion effect: more than 4%
erosion doesn't generate noise (except if you have 3M damaged foil)
Never include erosion repairs in your maintenance contracts
Sharing # 9
LEE is a concern to all developers and OEMs.
Anit-Ice solutions is still not fully developed.
Sharing # 10
Leading edge erosion is a huge problem. Its severity seems to be caused by various factors, such as where the WTG is placed and the quality of the blade manufactured.
S1 – Repowering
Sharing # 1
Repowering is little profitable without government benefits.
When repowering new laws and regulations must be applied which makes the project even more complex and expensive.
Life extension is in many cases a better solution.
Sharing # 2
Several requirements from the authority in terms of repowering or lifetime extension evaluation, country-specific.
It is part of a major challenge which is the strategy of end-of-life + evaluation of profitability from the different options at the end of life.
For LTE, which can be prioritized, ask for a clear maintenance plan, evaluation of the risk of failures of main components, replacement of the bolts from the tower, blades, etc.
Different ways to manage the new certificate body for LTE
Environmental constraints very important in different EU countries which lead to obstacles for repowering as less profitable caused by several curtailment like noise/bird/bat..
Type of PPA, revenue forecast, if some governments still offer FiT or not
No specific return on experience about revamping, unfortunately
Sharing # 3
Repowering projects need help and support for the government to be worth it; until then, Life extension is a better solution.
The market doesn't have the right solution for blade recycling.
Risk in case repowering is mandatory at a certain age (Spanish case)
The secondhand market that comes from repowering is not running yet
The Repowering Projects needs a global strategy in each country looking forwards in long term
Sharing # 4
The different legal frameworks in countries and land lease agreements for onshore are the key points in onshore, and for offshore, foundations and the end of regulatory income are the key points. For everyone, permitting time is very large.
Sharing # 5
Help is needed to make repowering profitable.
Portugal is an exception because there are feeding tariffs after the repowering that make repowering profitable, and the wind farms can increase their output power.
Wind farms with availability problems due to access to spare parts will be the next to be repowered
Problems due to the need for less manpower, as there will be fewer turbines to maintain.
Surrogacy of workers, difficult profitability, and increased friction with local authorities.
New regulation requirements force the change of the medium voltage network and the main transformer, increasing the CAPEX
Repowering means new risks: New environmental requirements.
Blade recycling is not a solution, just prototype but not a massive solution
Land issues will occur with owners who lose the turbine on their land but have a bigger one on their neighbour's land.
Sharing # 6
For the power plant planned to be repowered, the permits and selling of the turbines processes should start 2-3 years before the repowering itself.
Rather than technical problems (apart from the foundation and perhaps the towers) repowering might be required to increase generation and the profit with bigger turbines.
As long as the permits are available or able to be revised repowering should be evaluated for profit increase purposes.
Repowering can in different scales, either changing the whole turbine and the foundation or finding solutions and replacing the gearbox, generator and blades (hub ?) only.
Sharing # 7
Supplier tip: https://www.we4ce.eu/en/headlines/80/we4ce-patents-its-re-fit-blade-root-bushings blade root bushing info
S1 - Manage and Monitor Grease and Oil
Sharing # 1
Most of the operators are still in the mind of maintainers (repair fast) when we may have to shift into the asset manager (avoid failure).
My proposal is to develop a strategy for collecting common health data, set good cleanliness reference figures, and build the knowledge to evolve toward new mitigation techniques that would allow failures to be avoided.
Sharing # 2
Two positions: 1) Asset Manager: try to get any issue on the Main component. Insure that the lubricant is still in its initial condition => characteristic of the lubricant (Visco, additives). be aware of the cleanliness (external contaminant). Use another external filtering unit to help the internal filtering unit system which could be insufficient. 2) O&M position: monitor the wear information by trend.
For the grease (MB, BB), should a sample be taken to monitor the lubricant quality and cleanliness.
Sharing # 3
Everyone has different internal standards and strategy approaches.
Main Findings - Session 2
S2 - Real-Time Data & Predictive Analysis
Sharing # 1
The data that we are receiving is limited and started to be a business and it's turned to be critical to the wind turbine analysis.
The data is relevant to verify the values of O&M and preventive maintenance.
The first step should be data verification (availablity and quality). Availability is % of data collected.
Quality verify data out of range, frozen values and zeros
Sharing # 2
Access to the raw database, and high frequency data. as owner we should get access but difficult for sure in the real life.
Data quality is key and data reliability, automatic identification of missing data, availability
No big change in the industry at the moment with AI but something starting a few years ago
CMS data access, some rex about the platforms to be used as agregator of data like Onyx fleetmonitor
Small focus on eolotec and onyx blade bearing monitoring
Ping monitor for icing detection, good feeback from Energia
Sharing # 3
Data access is a concern for everyone. Good to understand how large asset owners operate in their performance analytics teams.
Sharing # 4
Data acquisition: focus on getting 1-s OPC data
Some OEMs are restricting access, but the future EU Data Act should ensure the owner gets access to the data
Sharing # 5
Good to hear on Life-Time-Extension companies that can do assessments. Also to hear GE is only OEM to take their large data lake value seriously.
S2 - Optimal Pitch Settings & Energy Yield
Sharing # 1
Skillsets important for self-performing pitch adjustments, possible to develop with a few 3rd party experts, but only a few options (mostly come from former OEMs and are done by larger operators)
Tricky to make adjustments when it is full scope, but should still develop a representative way to access performance (audit OEM)
Limits to acceptable optimization (depending upon risk appetite and competence), similar triggers for assessment of abnormal load conditions and devotion monitoring (can this be put into the standard? CMS?)
Sharing # 2
Inspecting blade positioning and the supporting hardware is key from an owner's perspective.
Using correct data to detect misalignments.
OEMs tend to provide 10-minute data, so 1-second data would be required to look at individual misalignments and neighbouring turbines for all three blades.
Fine-tuning should rather be done with the OEM instead of independently.
Owners and third parties can collaborate on data collection and analysis, but changes are to be made with OEM.
Ensure CIM/OEM notifications are implemented.
Sharing # 3
Finetuning pitch control: Owners need access to high-frequency data (1 second data). If an Owner wants to boost its asset, it won't be easy without the OEM since he does not know the limits regarding loading.
Pitch misalignment detection: ground based device tested by owners and worked well. Difficulty is on getting correction implemented by OEMs and assess AEP recovery.
Lacking monitoring on pitch system. “no CMS for rotor
Ability of OEM to react site people or service guys do not have proper skills related to rotor imbalance.
Owners must develop their own skills and inspect assets after maintenance.
Sharing # 4
Power can be increased with pitch settings, but this also increases the loads, which affects the life time.
Important thing is to analyze data and ensure there are no additional loads or vibrations that differ from other turbines in the site.
S2 - Managing O&M Costs
Sharing # 1
There are not enough ISPs to manage new platforms
Full Service is dead, and exclusions are becoming bigger with Siemens Gamesa and GE
Access to the supply chain reduces the cost
Offline oil filter reduces O&M costs
Availability performance as a system to control maintenance performance is expensive. Should we move to time response? Mean time between failure?
Volume and clusters reduce the cost
Reducing risk and uncertainty for maintenance reduces the cost
Sharing # 2
Do you perform maintenance depending on the age of the component? => NO
Off-line filter permits to decrease considerably oil change needs (from 3 to 1 ) AND better lubricate gearboxes even during turbine long stops, avoiding gearbox wearing
Sharing # 3
Reduce bureaucracy in the maintenance process between OEM / ISP technicians
Get out of Full Services needs: Technical skills, tools, supply chain
What we must do first is to understand the breakdown of cost in Full services...OEM don't give information. What is it inside the price?
If you want to reduce maintenance costs, internalize the risk (or part of it)
Sharing # 4
It is very valuable to share experiences with colleagues. The information I found most valuable is the challenge that some companies face to go self-performing and what company scale justifies that. Related to the problems of my own experience, we shared ideas.
Sharing # 5
You need a certain critical size before starting to internalize
What is your risk appetite? If you excluded MCR and you have one, can you deal with that?
What are the main drivers for O&M cost? The failure rate is an important one. They use both the occurrence and the costs linked to more repairs as well as the lost opportunity in energy lost. If you can be faster and better than the OEM, you can make a lot of money.
Logistics is a key element; you need a critical mass to make sure you can have scale effects in the logistics of the wind farms
You need the back office and infrastructure to deal with the logistics and support functions: purchasing, IT, warehousing, field support, etc.
S2 - Contract negotiations with OEMs
Sharing # 1
Require Turbine Configuration Sheet as part of TSA with full specification what is installed in each WTG.
From negotiations point of view you could show anonymous performance data between OEM's and tell that you don't trust the performance in the OEM and that they need to proof themselves.
Link PPA's to availability LD, not only to spot prices.
Add a cap on price indexation.
Add that you should always have the right to witness work.
Sharing # 2
Great insights and discussions around topics including self-performance, performance warranties, leveraging scope and duration of contracts, and understanding market dynamics that may affect risk profiles for both owners and OEMs.
It is interesting to follow Chinese OEMs and how the political agenda drives development in Europe.
It is important to have Employers' Requirements aligned in-house before engaging in TSA and SAA negotiations.
Sharing # 3
Bonus and variable fees in O&M service agreements do not help, as the local service teams do not benefit from them.
Lack of service technicians: Electricians and Mechanics should be available. It's about the poor payment of OEMs.
Technical documentation and access to SCADA: reverse engineering may help and is offered by some providers.
Technical documentation: it's the European OEMs that are reluctant to provide meaningful documentation. Chinese, Indian, and US's OEM's are more open.
Draft agreements: Usually owner's accept OEM's draft agreements, but define own rules, requirements, templates.
Sharing # 4
Possibility to negotiate with OEM during the SMA negotiations, different options of scope of work for different years that we can activate in the future
Possibility to have the OM done by a third party due to commercial reasons
Sharing # 5
It is difficult to get from the OEM's what you desire as they are dominant mainly and strong so it may require a big MW or a negotiation power in your possession to success from this perspective.
There is also risk of OEM's disappear from markets due to their financial problems so it should be necessary for these kind of worse case scenarios when negotiating contracts with them.
Sharing # 6
Negotiation timing related with TSA and scale are important.
Also, scope change according to the phases are important.
Sharing # 7
Market is moving to do more and more O&M hybrid models or in house
Sharing # 8
Smaller IPPs are signing long term contracts, very different what we are doing as Enel (short-term contracts). That makes the negotiation terms quite different.
S4 - Refurbished Components
Sharing # 1
Collaboration between power plants with the same turbine models to create an attractive business for the refurbishing companies and for creating parts warehouse. Individual operators might have a limited number of the same turbine models, so listing nearby projects with the same turbine models would make a reasonable fleet.
It might be difficult to assess the lifetime of a refurbished component.
Predictive methods (machine learning and/or reference from already broken components) for the parts/components to fail are important to know in advance if there is a potentially problematic component and order a refurbished one in advance without getting into the urgency.
Not only major components or mechanical components but also electronic components might be difficult to find. It is possible for some companies to reverse engineer these electronic components and manufacture them.
For certain main components of aged fleets, power plant decommissioning might be followed either through databases of turbine models and locations or through OEMs. OEM might like to buy components from decommissioning power plants to acquire the obsolete components.
A condition in new contracts is to provide all spare parts at least for the type certificate lifetime of the turbines (min 20 years). After a certain number of years, the OEM shouldn't be able to limit the suppliers from selling components directly to the operators.
It should be preferred to refurbished all components as much as possible instead of buying new ones, to decrease the carbon footprint of operating wind turbines, this should increase the number of refurbishment companies and the OEM's shouldn't be able limit them. This is the item we have planned to bring up in the EU Parliment to decrease the carbon footprint. :)
Sharing # 2
New supplier information for us
Amara: Marketplace for refurbished parts
Man Energy: Yaw gear up-tower repair
Doble transformer: customize transformer
Hitachi: customize transformer, adding sensor to check the leakage
Sharing # 3
The availability of some spare parts and main components is getting more and more challenging, and neither refurbished nor new ones are available. The supply chain lacks transparency; owners don't have information when a component becomes obsolete until it is actually needed.
Some manufacturers are not allowed to deal directly with owners or refurbish or manufacture components because of contracts with OEMs.
A shared stock setup might be a solution, though it needs initiative from the owners, will and a lot of coordination.
In general, it does not look promising, and the issue will only get bigger as turbines are getting older.
Sharing # 4
Different strategies to refurbishing - internal and external engineering.
Sharing # 5
2 standards relative to lifetime extension include a checklist on appendix:
IEC 61400-28
DNV-ST-0262
S2 - Gearbox & Drivetrain
Sharing # 1
Main bearing, while not an issue at our sites, is an important issue with others.
Sharing # 2
Need for sharing failure cases in the drive train to have detailed statistics per turbine brand, type and version, per component brand and type to allow a statistically accurate result to be used to challenge the OEMs and potentially the certification process
Sharing # 3
We have issues with the main bearing on our SGRE turbine. I learned that the problem with the front bearing might be transported to the gearbox. It might be seen on the torque arm. The position of the torque arm can be found if we measure exactly. A change of this position can be an early warning of bearing issues.
Sharing # 5
Main bearing failure
Generator bearing failure due to mid-alignment.
Lubrication manufacturers
S2 - Real loads assessment at site assessment level
Sharing # 1
Wind digital twins with load monitoring reduce uncertainty, but the cost-benefit of implementing will depend on the number of turbines in the fleet and margins between the predicted and desired asset life.
Sharing # 2
There is a great interest in negotiating direct accessibility of load data on the blades in the contract with the O&M
Sharing # 3
Use generic models to verify the load conditions of any wind farm in order to verify the Consumed Life of the wind Turbine
Try to use all the information saved during the operational life of the wind farm
Sensoring the wind turbine only to solve some reliability issues
Load assessment can be used to analyze other topics as curtailments, etc.
Sharing # 4
The added value of extremely accurate and expensive measurement campaigns can be very limited. In the end, the need for inspections at 28 years or 30 does not justify the cost.
Real wind conditions on site (met mast, lidar) really helpful.
Curtailments (approx 25% of rated power) are not recommended as it add heavy loads to the wtg
S2 - KPIs in wind farm operations
Sharing # 1
There are several challenges to utilize KPI
Which KPI yo be used, how to collect and handle data, how to calculate KPIs, how to reflect it to maintenance and etc.
Sharing # 2
The contract availability KPIs are changing from being time based to energy-based recommendation is to keep the formula as simple as possible, so the negotiations just go for exclusions.
Sharing # 3
Full-service O&M contracts: Not so easy to monitor KPIs, you can mainly optimize the contract terms
ISPs work well (even better than OEMs), it is a matter of negotiating a good service level
In certain mid-term O&M contracts (5 years), there is the possibility of optimizing the cost based on observations of the real cost incurred (difficult to do with some providers)
IC61400 production ratio – Your KPI is only good as long as your expected production is accurate, and this is not too easy to do
Sometimes, EYA is not accurate, and this generates many deviations which are hard to explain
Most of owners use P50 as reference production, which is by definition quite volatile
Some owners are moving from energy-based availability to time-based energy, especially in cases in which there is voluntary curtailment due to negative prices
Some owners are doing internal checking of main components, as they don’t trust the contractor
Sharing # 4
Main KPI's are the common ones: availability, MTTR, etc.
Optimize contracts/renegotiate at moments when possible, build in 'step-out' moments, or for example, when there is a lifetime extension
Work with bonus/malus with OEM to stimulate the party to create better KPIs. However, experience is that this incentive is not enough for OEMs to reach higher availability.
But you can still have influence on KPIs and you can steer/influence on lower cost in long-term contracts: define optimized maintenance strategy, make use of (re)negotiation moments in your contract.
What can also be a KPI: prediction ratio. Which is: power curve based on site conditions vs. real power curve - track deviations. However, the difficulty is which reference power curve you use - air density, for example, changes every 10 minutes. Mainly in difficult environments.
What is also related to KPI is the part of loss of production that remains after deducting the known factors - this is the part that keeps unexplained. Deep dive into this when this ratio gets higher.
If you don’t have a long-term contract but if you do more mtc by the team yourself - challenge to set KPIs as well. Go for time or energy based for example? Making this decision really depends on site conditions (think about curtailments, which become more and more common)
Main Findings - session 3
S3 - Digitalizing O&M Workflows
Sharing # 1
Scale up, proper project management, fine understanding on creating kpis: these are some of critical points to get an smooth adoption of new digital tools
Sharing # 2
Digitalizing O&M Workflows are difficult to quantify to investors.
Staff adopting systems is difficult.
Current systems being used by owners are either expensive or multiple systems are required.
OEM's are not always keen to integrate their systems.
Sharing # 3
To digitalize and automatism you need to compromise precision.
User commitment and alignment is key to the success of tool.
Adoption is essential, process analysis should always come first.
Sharing # 4
It looks everyone suffers system integration for renewables energy O&M management and improvement.
Add to that, quantification of the system is also important and difficult part.
Sharing # 5
Anemo Analytcs good performance products.
Skyspecs and Sulzer Schmid good blade management system.
Challenging to get API towards OEM's to get maintenance reports.
Sharing # 6
How to measure the performance of digitalization?
Manhours reduction
Too much digitalization could reduce the feeling about what is going on at the WF
Problems of communication must be solved first.
Digitalization without communication is nothing
Importance of a communication assessment
Involve people who will use the digital tools
Procedures are more important than tools
S3 - CMS in wind farm operations
Sharing # 1
Pushing OEM to do the work based on CMS info is useful. Putting together a case showing they did not act on time can help get them to work in the future.
Skyspecs service as a global CMS platform is reported to be excellent. Not so good experience with Onyx
Difficulties in getting CMS data during the warranty period still is a problem. Dealing with this issue when the service agreement is discussed helps
Making sure the client gets full access to raw data and to parameters in the CMS is a must and needs to be considered when choosing a CMS
Sharing # 2
Onyx VS Skyspecks comparison:
Same same platform
Same same data collection quality
No direct data collection from EcoCMS (all is trough Onyx platform)
Too much alarms with Onyx
EU data act: 09/2025
When a O&M doesn't take in consideration our CMS analysis: send a official letter saying "if we are right, we will ask you compensation"
SKF too expensive
Bachman ticketing service is not working for all of us
Sharing # 3
Good Software for CMS data analysis.
Sharing # 4
Onyx and Skyspecs are the two main options for CMS multi/platform management.
Many owners do their own analysis on top of the contracted CMS analysis company
Sharing # 5
The discussion was mainly about icing detection systems.
Sharing # 6
End of warranty difficult with OEM. OEMs have tactics to deal with claims, e.g. wear and tear.
Scope of inspection: various depending on the length of warranty term and whether full scope contract is following inspection
Standards: IEC61400-28 will be issued at the end of 2024. This standard has a checklist in the appendices.
The failure rate is difficult to accurately predict for prioritising inspection of certain components. Ie cost of replacement drives priority for owners.
BSH requires 25% of offshore turbines to be inspected per annum. This can be used as part of an EOW campaign.
Geographical variations between OEM approach to end of warranty and statutory requirements vary from country to country.
Various successes of claims between owners.
Use serial defect claims as a negotiating tool, as they are hard to prove.
Legal teams can be involved to write contractual letters and if no positive response from OEM then a monetary claim can be made for remediation by the owner.
Technical documents are difficult to get if not negotiated in the turbine supply agreement.
Even if documentation is in the contract, the OEM will resist is during this to owners.
Detailed documentation is needed for gearbox internal inspections for example.
S3 – Lightning – Protection, Repair & Claims
Sharing # 1
The card can only read Lightning strikes above 200 kA
Sharing # 2
Installing a lightning measurement system in each turbine can be very useful. However, it depends on how your contract is written. If the contract specifies a specified level of strike intensity for which the OEM has a warranty, it is useful. If you have a contract where all lightning goes to the owner, frequent inspections of the LPS will be a better idea.
Sharing # 3
Difficulty evaluating systems and claiming issues when data is not supplied by OEM, seen intolerances and failed points within the circuit (cables, blades root connection, LTU mostly)
Discussion on utilizing IEC standards -24 and -1 to uphold sharing of information and when to inspect visually annual and do measurements every two years and evaluations through internal and external inspection (for strikes/arching), measurements for changes in contract/EOW
Solution systems for poor LPS systems such as 2ndary installed monitoring system, improved brush system for G90 LTUs, Vestas V2 improved cable systems for carbon blades.
Sharing # 4
It’s essential to conduct regular inspections of the LPS system. If any faults are detected, damage caused by lightning can easily be attributed to the manufacturer until the fault is repaired.
Sharing # 5
While lightning is mostly excluded risk, one needs to ensure that the LPS design indeed confirms that. The faulty design could mean that the supplier is still accountable.
Sharing # 6
SGRE 4.X: cables are installed during manufacturing to measure the temperature during curing, but are not removed afterwards and get struck by lightning
Vestas OLPS really deficient, flashovers from the carbon spar to the down conductor at around 10m from the root
S3 – Remote Inspections – Robotics & Drones
Sharing # 1
Remote inspections with drones have become faster;5-7 turbines' blades inspection can be done in one day.
Drone inspections are important as a safety measure decreasing risks with rope access and similar inspection works.
Internal inspection of the blades is important to detect some crack early in their propagation without the need to wait for the crack to reach the outside of the blade.
But in any case, blades' inside and out inspections are both important.
Drones have developed considerably, but especially for internal inspections software development is to be progress further.
Thermal cameras with drones might be used to control the anti-icing systems on the blades.
There are already one or two companies who can do ultrasonic inspection with drone/crawler robots.
It is an option to by the drones and the software instead of buying the service.
It will be followed up if autonomous usage of drones is legistlatively possible and will be informed through O2O platforms if possible.
Drones might be used for tower inspections as well, switchyard and overheadline thermal inspections.
Is an EL test possible with drones on Solar Power Plant.
Sharing # 2
There is a lot of solution in the market, Different companies different solutions, believe in this and the biggest obstacle is to find a good software that could work for all applications indicating damages from both inside and outside in a 3d picture.
S3 - Access to SCADA & Controller
Sharing # 1
It's different the SCADA and the controller and it is important to understand the scope of the company.
If the focus is assets management, the focus is SCADA, but if the focus is maintenance, the focus should be the controller.
The turbine manufacturer offers only a opc access.
There are options to rewrite the Controller software with options like Nordik Wind technology but there are not many references in the market
Sharing # 2
All operators need full controller access post-O&M contract expiration, and certain Chinese OEMs are offering this.
S3 - Noise - issues, causes and solutions
Sharing # 1
Regarding noise issues on receptors, the methodology of measurement and thresholds are really country-specific. The minimum distance in Brazil from the closest dwellings is 400m, which is short.
Icing detection and blade damage detection by using Ping solution, good feedback.
Financial compensation with residents who complaint, be careful and make the agreement very robust.
Methodology of measurement
Yaw noise issue on Senvion MM and GE 3.X
S3 - Supplying Main Components
Sharing # 2
Specific Tools are one of the more difficult items to get, exclusivity and price
Sharing # 3
It is important to find alternative provider for the critical spare parts but as well as the documentation and special tools.
The refurbishment is also ok from the OEM's to supply.
Exclusivity agreements need to be considered when it comes to procurement discussions with OEM's.
Sharing # 5
Focus on contracts for older assets is important.
Sharing # 6
Sourcing Main Components still is a challenge, even large asset owners are struggling to completely operate independently and are depended on the WTG OEMs.
We need to collaborate more amongst ourselves to overcome this challenge.
Sharing # 7
It is challenging to source spare parts outside OEM, and OEMs are charging premium prices.
Shared stock for owners of the same platform might be a good solution.
Sharing # 8
For many OEMs, even if you exclude main components, you are still dependent on the OEM because they are the only ones providing the main component.
How do you manage your stock if you want to have a stock - how to estimate the stock amounts?For stock amounts (arranged by company itself) the experience is that the warranty is between 3-5 years.
How the amount of stock parts is decided: only learn about own experiences/have conversation with OEM.
Consideration: if you need a new main component but you are facing the last operational years: consider if you want to buy an aftermarket part of refurbished part take this into account for your main component strategy.
In Denmark and Germany there are several repair shops where you also get guarantee on the repaired main component.
Blade refurbishment/aftermarket: there is a market for it but not really common yet, spares.
Main Findings - session 4
S4 - Lifetime extension for wind assets
Sharing # 1
Most operators at 18-24 years looking to benchmark and plan for life extension 30-45 years.
Plan for analysis to formulate maintenance based on 10 year and then add additional inspections related to top impacted inspection;modeling mostly external with a few operators self-performing inspections, aeroelastic modeling, and FMEA / risk assessment in-house.
Discussion on pros and cons of different reason to repower, keep running turbines, and repower lite based on site limitations, market, environmental and remaining margin in components. Each operator has different levels of risk tolerance and appetite for risk.
Sharing # 2
Life time extension assessment would be done especially and in the first place for structural components and safety systems.
A life time extension might mean only the control and maintaining these systems on the one end of the spectrum to putting in more CAPEX related to mechanical componants' replacements and major repair.
In the coming years increasing number of turbines will reach end of their lifetime, so the subject will be more popular.
First we have to set a baseline for the project with permits, legistlatively and from the partners point of view. Then if it is possible structurally, financially, legistlatively.
There are some technological solutions we can work on like installing additional sensors, using digital twins in order to better prepare for the end of the lifetime. But the efficiency of these solutions are yet questionable and their complexity would be high.
Machine learning models might prove useful for determining conditions of the main components. The models would need a selective set of data with the participation of engineering groups not only data analysts to improve the reliability of the outputs.
A hybrid approach of repowering and lifetime extenions to optimize the benefit with lower capex. The decommissioned turbines might be sold or their components might be used as spares.
Scrap value of a turbine would further decrease as a lifetime of a turbine is extended. This should be taken into consideration.
An upgrade with the lifetime extension might be possible if developed with the oem and a supplier like in the case of V90's. This is also done more popularly in the US.
Sharing # 3
2 kind of concerns : Spares availability / structures condition . the firts mandatory point is security and integrity of the machine.
Key parts to take care : blades, tower structure, frames, fundation. (the other parts / drive train, etc.. is quite well followed as usual)
No big investment needed to be efficiant financialy , better less cost O&M and taking care of components. curtailment possible to avoid to much wering by "performance required " behavior (ie : slowing down the pitch or yaw).
Preparing the long term lifetime from the begining , by requiring less performance and taking care from start. (ie avoid power+ or EnergyTrust)
Sharing # 4
General approach of assessment broken up to Structural, safety, reliability (site inspection also very important)
Likely legislation will flow to other regions to regulate life extension approval including additional servicing
Twin models seem to be the gold standard applied in early years of the asset to provide live status of available life
Sharing # 5
The impact of start/stop in mainly see in Blade. An equivalent of time consumption per start/stop is possible to define.
Sharing # 6
How curtailments eat into lifetime. And how to optimize your curtailment regime.
Sharing # 7
Recommended to start planning the life extension approx 5 years before.
Special check list for the maintenance needs to be done based on failure mode analysis.
Spare parts management for possibility of obsolete platforms
S4 - Main component repairs and replacement methods
Sharing # 1
Needs to push the up-tower repair to reduce de cost.
Ask the OEM to identity de up-tower catalog to clarify the different scope between Full Service and Risk Services.
Idea for O2O: share workshop for each major component, Wind turbine model and country.
Needs in mechanical workshop are higher than electric ones. We're loosing players for mechanical repairs
Are OEMs blocking repair shops from working directly with companies?
Sharing # 2
Hard to find secure parts and tools.
Sharing # 3
Some good suppliers for 2nd hand market.
Sharing # 4
To repair the GBX Sermec could be a good possibility to explore.
Sharing # 5
Tooling for major components is a big issue for most of the participants, where the OEMs are not selling or renting those tools.
Contact of companies capable to reverse engineer or develop new tools is required.
Sharing # 6
Tool sourcing is still one of the complicated items
Sharing # 7
Share information between members about workshops that can repair major components: Gearboxes: Moventeas, Multigear
Importance of new procedures to replace major components in new big turbines
CE certification can be lost if we replace a major component with a different one?
The machinery directive is for the turbine as is, according turbine configuration sheet
Sharing # 8
Mainly 5X onshore type with pre-tensioning issues, Vortex damage on blades, breaking bolts.
2. Supplier data base for main components to calculate MTBF stats.
S4 - Increase power output
Sharing # 1
Power increase offered from some turbine providers has a neglectable increase which is difficult to measure and in more of the cases insede the uncertainty of the measurements.
A strong contract is required in which the participation of the O&M team should be included in other to pay twice for the service (bonus from O&M and the service yo improve the power or to avoid that the O&M team deletes the improvements done in te software.
Verify the nosel alignment and calibration of wind sensors could also improve the performance of the turbines.
A better and active follow up of O&M activities may also reduce the stop times and all the monitoring or control room team should be involved and commited with it.
Bird and bat detection also impacts the out power in wind turbines. There is possible to install bird detector sensors or have people watching for them. In the case of bats those sensors are currently not used, however, there are some tests on going
Sharing # 2
How to ensure that the software upgrades don't get erased after some software maintenance? --> Need access to the WTG parameters
Very active O&M contractor management, call them when there is an alarm to make sure they go quickly to site
Sharing # 3
Possibility of using Wind Eagle (to measure yaw alignment): Not much experience
Birds and bats curtailmentOEM trying to sell owners features of the product which should already be there
It can happen that the OEM charges for an improvement, and then gets a bonus (double billing)
Struggle with grid curtailment
S4 - Blade Bearings
There is very detailed sharing for this roundtable with name of wind farms, companies etc. This has been shared with the participants but is not shared here.
Sharing # 1
Blade bearing failure modes can be various.
Ovalisation, lack of bolt preload, lack of design safety factors, contamination of the rolling contact surfaces.
Lightning could also be a factor where no blade bearing spark gap is installed but no info available on what extent lightning can affect bearing life.
Onyx and Eolotec have blade bearing CMS but no results available.
Owners looking for alternatives to SGRE CMBB for Senvion MM platform.
Sharing # 2
Joint action with several owners needed to push the OEM to provide BBR specs including clearance safety limits
Sharing # 3
Good grease samples do not necessary mean no issues on blade bearings.
S4 - Renewables & Storage
Sharing # 1
Response time instead of availability depending on the requirements and constraints
Low maintenance required
What is a good availability for BESS?
What is the number of technicians needed?
Sharing # 2
No parties have many experience with battery systems.
Some parties are exploring options to add BESS to windfarm - having conversations/asking for quotations for maintenance for the BESS system.
Expectation is that less maintenance is needed on BESS -mainly visual inspections.
However troubleshooting can also be needed - challenge/question is if wind technicians could do this maintenance so you can combine it with your windfarm.
Biggest challenges: find synergies, find out how many technicians you need for how many MW's battery, hard to challenge technicians because of lack of experience. What can be done is ask for references at BESS OEM parties, even if they only have experience with other/larger/smaller projecs.
Another challenge is: how critical is it when the response time is not followed up? Is working with a availability % most optimal? Or should we work with response times.
An idea could also be to arrange a contractual bonus malus based on electricity prices.
Sharing # 3
Everyone at the table is in the same situation of looking into storage systems but not having any in operation yet. We all seem to have similar challenges and questions, so we have a lot of questions but not all the answers
Challenges brought up: How much work do battery systems need in operation?
How much technician resources need to be allocated for operation?
How to formulate OM contracts?
Availability based contracts, and whsy os normal Availability?
Should a response time be specified in contracts for troubleshooting how to formulate that?
Is it possible to get reference project from the battery manufacturers?
S4 - AI in Wind Farm Operations
Sharing # 1
Several usage for renewable energy business such data (report documents etc.) management and data analysis (forecast, optimization of revenue etc.) are mentioned and discussed.
It might be good to start using AI from simple daily purpose not only advanced data analysis purpose.
Sharing # 2
AI is still very new in the wind industry, and it seems the OEM's have the upper hand since they have all the data.
Sharing # 3
AI is a new area in the business, the general applications are the blade inspections by drone equiped by AI softwares, some asset management tools, etc.
Failure rate prediction from AI based tools would be nice.
Sharing # 4
Very valuable to share experiences with colleagues.
The information I found most valuable is that I see that many companies are looking for this but the results so far are limited to blade inspections and in some cases with contract management and asset performance.
The main findings from the turbine-specific roundtables - Session 5 - are too detailed and often directly linked to operators or wind farms. These main findings has already be shared with the participants but will not be shared in this more public and general version.